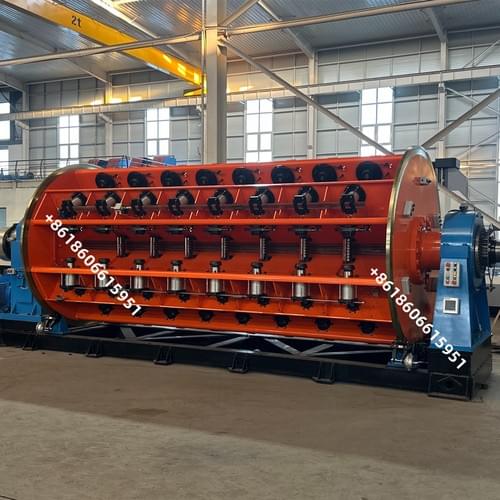
Rigid Type Assembling Armouring Line JLK-500/96 Flat Wire
Model Number:500/48+48
Payment & Shipping Terms: EXW/FOB
Minimum Order Quantity:1 SET
Price: By Negotiation
Packaging Details:Export Packing
Delivery Time:120 Working Days
Payment Terms: L/C, D/A, D/P, T/T, or By Negotiation
Rigid Type Assembling Armouring Line JLK-500/96 Flat Wire
1. Main Feature:
This machine is mainly used for armoring high-pressure hose. Final hose is used for conveying of offshore oil, natural gas and all kinds of high-pressure hose on land. It consist of pay-off stand, steel wire armoring machine, capstan, electrical control system and take-up stand.
Steel wire pay-off tension is controlled by mechanical friction(adjustable) or pneumatic friction(constant tension and adjustable).Stranding cage adopts rigid frame type with good rigidity.
Each part is driven by independent motor. It adopts SIEMENS PLC to unified control and manage the working condition of each motor. The rotating speed and stranding pitch have be changed by stepless, and can be adjusted and dispalyed on the touch screen.
2. Main technical parameter:
- Low carbon steel wire: Φ1.0-Φ3.15mm
- Max core dia. Before armouring:≤Φ80mm
- Rotation speed:72.5r/min(working speed)
- Armoring pitch Stepless adjust on PLC
- Main stranding motor power:90kw (AC variable frequency motor)
- Φ600x2 non-metallic taping machine speed:500r/min
- Non-metallic taping machine pitch:Stepless adjust
- Non-metallic taping machine motor power:11kw (AC variable frequency motor)
- Φ800x2 metallic taping machine speed:450r/min
- Metallic taping machine pitch:Stepless adjust
- Metallic taping machine motor power:22kw (AC variable frequency motor)
- Max traction force:5 T
- Max traction line speed:30m/min
- Pneumatic caterpillar motor power:37kw (AC variable frequency motor)
- Pay-off bobbin size in cage:PN500(customer bobbin drawing)
- Center Pay-off bobbin size:PN1600-PN3150
- Take-up bobbin size:PN1600-PN3150
- Machine center high:1000mm
- Applicable cable reel specification: PND500mm (to be executed according to the buyer's drawings)
- Maximum speed of stranding (full load): 72.5r/min
- Twisting cage pitch (can be set on the touch screen): stepless and adjustable
- Twisted motor power: 90KW (AC variable frequency motor)
- The first section of the stranding cage is equipped with a 48 hole distribution board, and the second section of the stranding cage is equipped with 84 pre twisted heads and distribution reels
- Each section of the hinge is driven by a separate AC motor through a dedicated gearbox, which can rotate left and right. The gearbox is equipped with high and low speed 2 gears, which are used for high speed during normal stranding and slow speed during disc changing. The main motor drives the stranding body to rotate slowly, and the automatic positioning of the upper disc position is switched using a handle.
- Double supports are provided for the front and rear support frames of the entire hinge, with seamless steel pipe support in the middle. The frame body is mainly made by high-strength welding of the steel plate connection surface after processing, and the welded overall frame is subjected to high-temperature annealing in the annealing furnace to accelerate the aging treatment of the deformation and stress generated by the steel plate welding. After 72 hours, it naturally cools to the natural temperature, effectively enhancing the strength of the entire frame. There is machining allowance left for the brake surface of the hinge body, and there is allowance left for the top installation hole. After all the holes are fully drilled, machined, and milled at the gantry machining center, they are then precision turned on a heavy-duty horizontal lathe. The hinge base plate is welded with rectangular tubes, which effectively enhances the stability of the hinge compared to ordinary channel steel base plates and is more suitable for high-speed rotation of the hinge. The dynamic balance experiment after the assembly of the hinge meets the requirements of high-speed and stable operation.
- The tension of single line pay-off is controlled by mechanical friction tension, and the tension is manually adjusted.
- The wire reel adopts end shaft pneumatic clamping, and the cylinder clamps the wire reel from bottom to top, making it easy for the wire reel to move up and down. After the wire coil is clamped, the pneumatic interlocking mechanical safety locking mechanism is used to achieve linkage and stop
- Using digital quantity detection to detect wire breakage can accurately determine the wire breakage signal of any reel in each section of the twisted body, and display which section it is on the touch screen of the main operating platform. The stopping length for wire breakage detection is within 2M (at a line speed of 20M/MIN), significantly improving the accuracy and accuracy of wire breakage detection, ensuring detection accuracy.
- The hanging operation of each section of the winch body adopts the slow speed gear on the gearbox, which is driven by the main motor to drive the winch body to rotate slowly for slow positioning. A proximity switch is used to detect the positioning pulse signal, ensuring accurate hanging position.
- Each section of the twisted body adopts a wall type protective fence, which is fixed.
- 4Each section of the hinge is equipped with a set of hydraulic side lower hanging device.
- The stranding body is equipped with a set of 84 head single wire pre forming device, which is used for circular single wire stranding to ensure that the single wire is not loose after the conductor cross-section is disconnected after stranding.
- The single section twisted cage of this machine is equipped with a central wire guard tube.

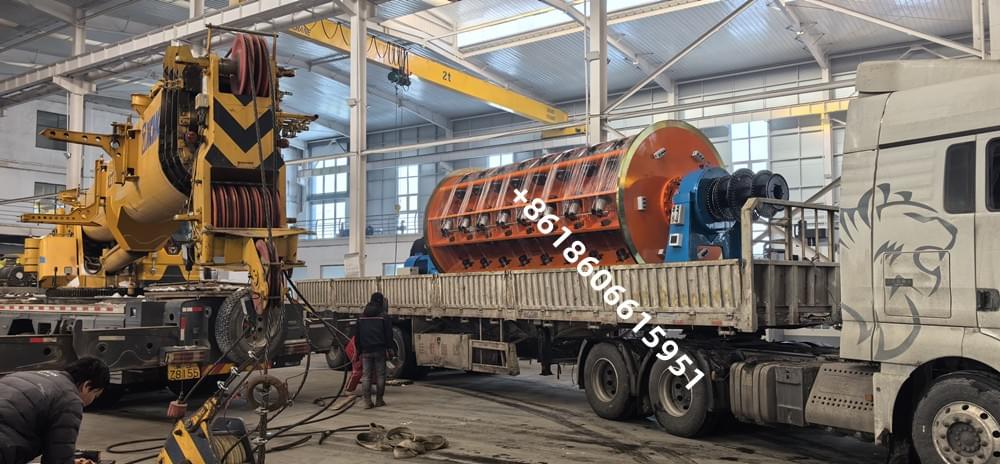