How to make the milliken conductor?
How to make the milliken conductor?
How to make the Milliken conductor?
1.What is Milliken conductor?
For example, the conductor can be directly twisted into an 800mm², It can also be made into 5 sector strand blocks through
single wire stranding, separated by separating paper, and then the 5 strand blocks are cabled into a 5 segmented circular conductor, the latter is called the milliken conductor. Generally,the voltage grade of the split(milliken) conductor: 66kV, 110kV, 220kV, 500kV power cable.
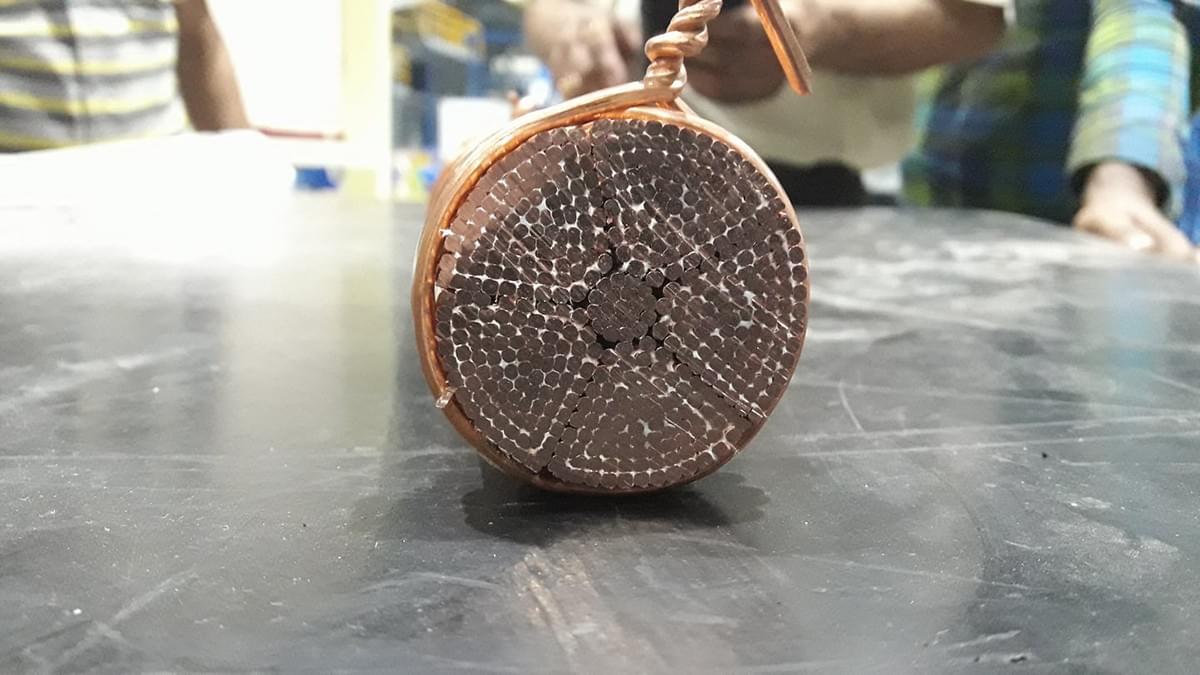
2. The structure of Milliken conductor:
The main forms of split conductors include 4 sections, 5 sections, 6 sections and 7 sections. The 5 divisions are the most widely used conductors in China, as shown in Figure 1. GB/T3956-2008 stipulates that the sectional area of the split conductor is 800mm2-2500mm2, as shown in Table 1. However, some enterprises have manufactured the split conductor with a sectional area of 3000mm2, or even 3500mm2, but only 2500mm2 is specified in this standard.China's GB/T3956-2008 is formulated with reference to IEC 60228-2004. With the technical progress of the cable industry, it is believed that more and more enterprises will be able to produce 3000mm2 and above large cross-section split conductors, so it will speed up the revision of relevant standards. It is believed that the future relevant standards will add restrictions on the range of sectional area of split conductors and related parameter descriptions.
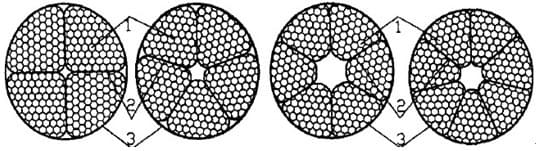
3. Under what conditions are milliken conductors used?
When the cable operates under high voltage and current, the AC current tends to flow on the conductor surface (skin effect). In addition, the magnetic field generated by adjacent cables will interfere with the current distribution in the conductor (proximity effect). These influences will lead to the increase of conductor resistance, which makes the increase of conductor resistance under
alternating current condition more obvious than that under direct current condition. Therefore, the typical "milliken conductor" structure can be used for the design of large cross-section conductor.
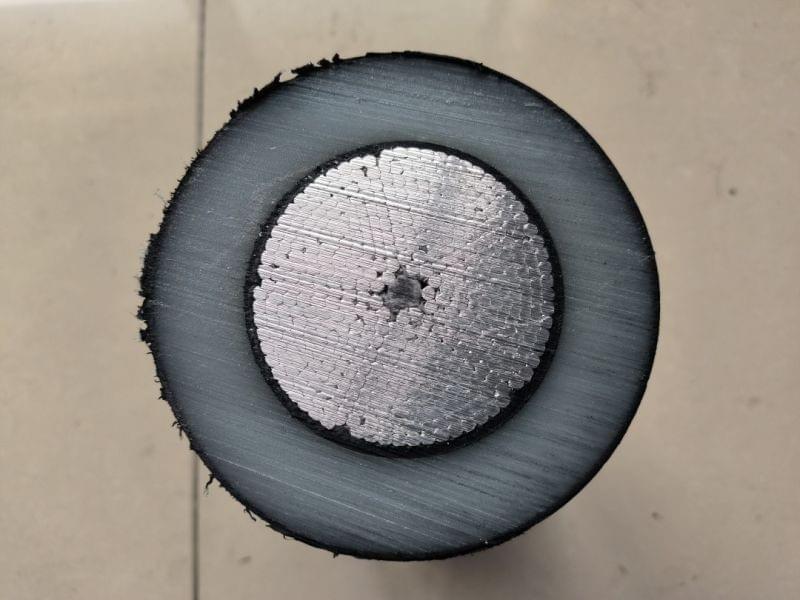
4. What machine produces milliken conductors?
The split conductor is not produced by aseparate machine, but is fabricated by assembling a specific equipment "Rotating prespiralled compactingUnit" during the "rigid stranding machine" stranding process. The specific functions of this equipment are as follows:
- Each cageis equipped with a single wire closing device, and the wire closing mold base is a quick opening design
- Eachcage of 12. 18. 24 reels is equipped with a rotary compacting device for the
rolling of split conductor (Milliken conductor). - Pre-twistingpitch: 1850-2050mm (provided by the customer)
- Drivemotor power: 4kw AC
- Rotationdirection: Z & S Working principle:The rotary molding device is driven by the reduction motor, and the PLC coordinates the inverter and brake unit to complete the synchronization of starting, stopping and other operations with the host machine, so as to ensure the stability of the prefabricated pitch. Each group of compacting holder can adjust the angle in the cable circumferential direction in the positive and negative direction, and can adjust it back and forth in the cable traveling direction to adapt to the rolling of split conductors.
For example, the rigid stranding machine 1+6+12+18+24 is used as an example. The 6 reels adopt a wire
closing die base, and the "rotary compacting device" is placed behind the pre deformation heads of 12, 18 and 24 reels, its task is to rotate the strand sector in order to form a spiral in that sector or its own option/laying length. This lay length is useful when connecting later during laying. When you purchase a rigid steel strand machine, you will certainly provide this function. If you don't want Milliken to become a conductor, just select the "Straight Line" function, and the price of the machine will be cheaper. The role of pre installed rollers is very physical. The key to life and Milliken's success starts here.
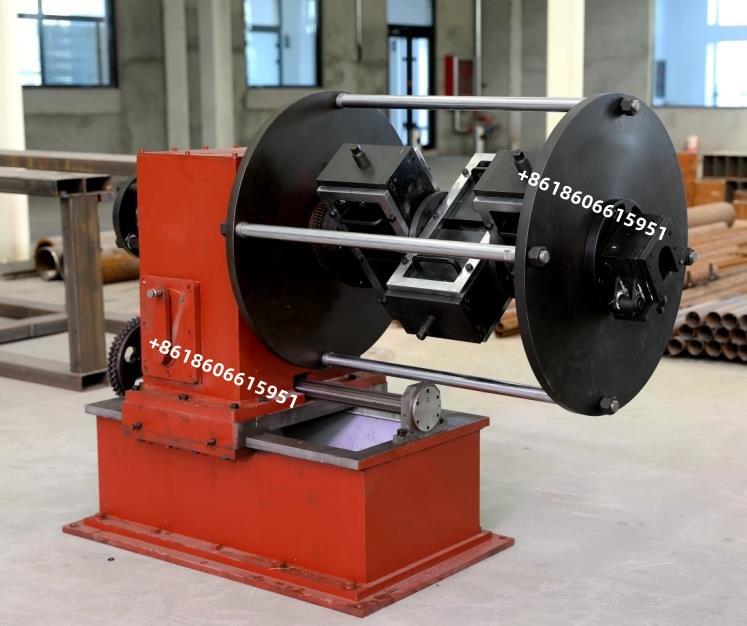
BEYDE's rigid frame strander adopts the sub motor drive mode. Each stranding cage, capstan and take-up are driven by a separate motor. The PLC is uniformly controlled, and the pitch can be adjusted steplessly on the PLC. The speed is up to 230 r/min, and the stranding process of copper aluminum wire requires perfect matching. At the same time, it is equipped with an automatic loading reel system, which is easy to operate and saves production time. The main electrical accessories of the machine are all international famous brands such as Siemens and Schneider etc.
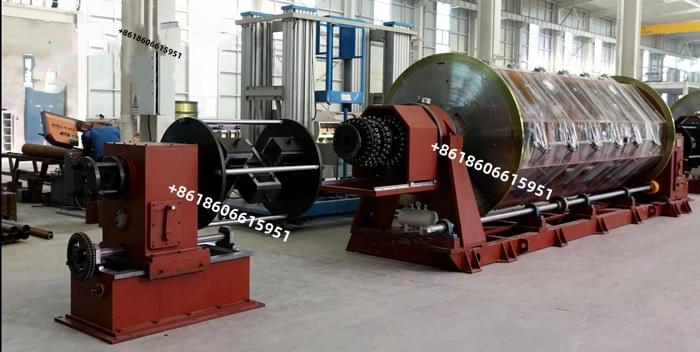
Forthe sector cable cabling problem after the production of split conductor, the "Drum Twister" is required to complete it. This is the problem we will discuss next. Please pay attention to the size.
If you have any opinion, welcome to discuss with